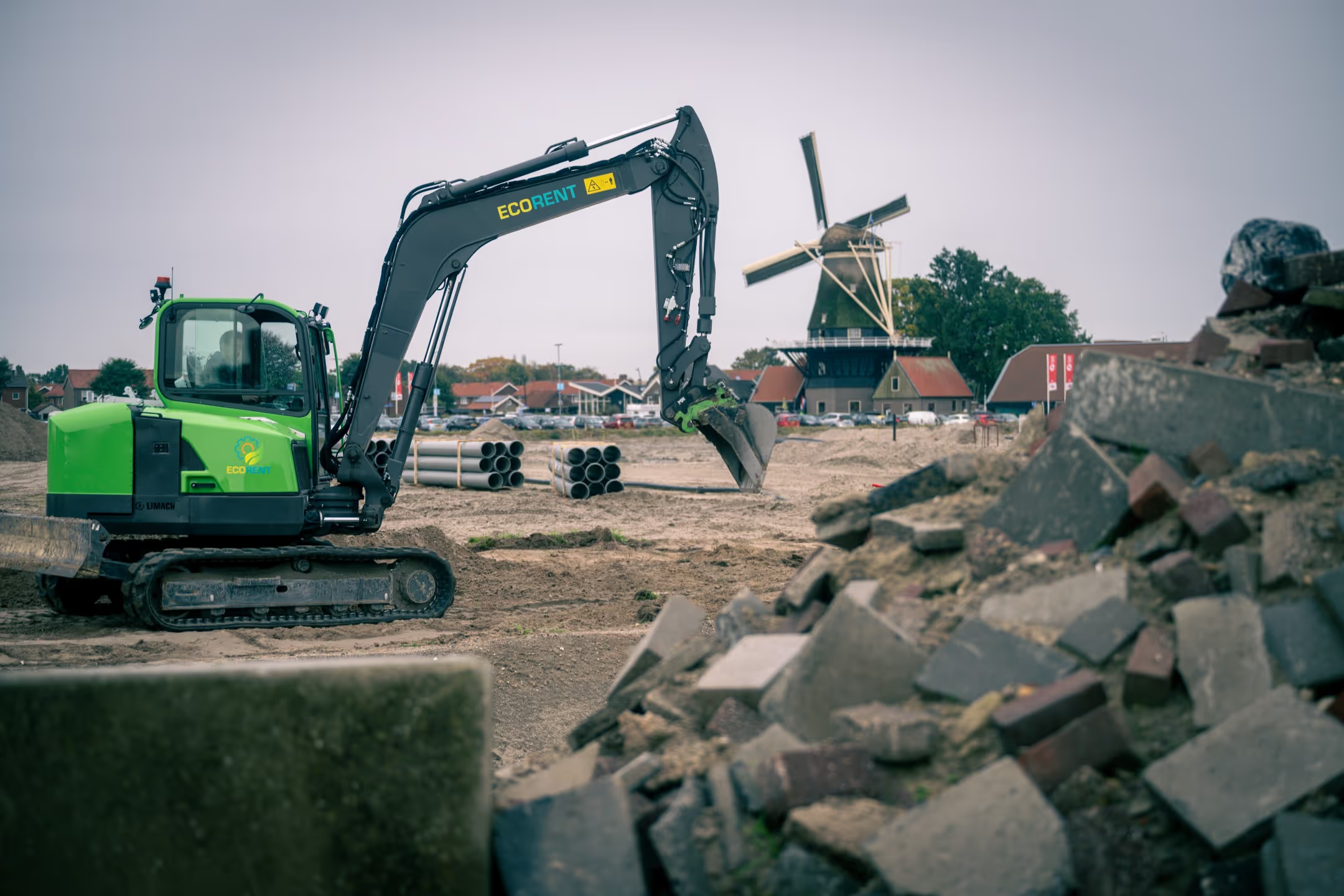
Wenn man auf dieser Sandfläche ganz still ist, hört man in der Ferne das Pfeifen der Delfine. Denn der Ort, an dem das neue nachhaltige Bauprojekt namens Waterfront Harderwijk entsteht, liegt unweit des Dolfinariums in Harderwijk. Und apropos Stille: Man hört kaum, dass die Siers-Gruppe hier ebenfalls tätig ist. Vorarbeiter Arjan Wesselink und sein Team arbeiten hier nämlich in aller Stille daran, die Wärmeversorgung für das Wohnviertel zu installieren. Dies geschieht größtenteils elektrisch und ist somit nicht nur nahezu geräuschlos, sondern auch emissionsfrei.
Es gibt noch etwas Besonderes an dieser Baustelle in Harderwijk: Dies ist der Standort der ehemaligen Asbestfabrik Asbestona Harderwijk. Im Auftrag der Gemeinde Harderwijk wurde der Boden aus Sicherheitsgründen vollständig saniert. Die obersten Meterschichten wurden sicher entfernt und auf den alten Boden eine Trennschutzfolie aufgebracht. Die Oberfläche wurde anschließend mit sauberem, gelbem Sand aufgefüllt. All dies geschah, bevor unsere Mitarbeiter mit der Arbeit begannen.
Unter der Trennfolie fanden keine Arbeiten statt. Allerdings war bei der geplanten gesteuerten Bohrung, durchgeführt von unserer Tochtergesellschaft SWST, kein Entkommen möglich. Die HDD-Bohrung durchquerte den kontaminierten Bereich unter dem Wasserlauf zum Rathaus. Die beim Bohren verwendete Bohrflüssigkeit wurde als asbestverdächtiges Material betrachtet und bis zur Untersuchung separat in Containern gelagert. Nach Prüfung stellte sich heraus, dass das Bentonit tatsächlich eine große Menge an Asbest enthielt. Umso besser, dass hier mit großer Sorgfalt gearbeitet wurde.
NTP hat die Arbeiten im Zusammenhang mit der Kontamination begleitet. Während der Arbeiten unter der Trennfolie (im kontaminierten Bereich) war auch ein DLP (Deskundig Leidinggevende Projecten verontreinigde grond) anwesend.
Nach allen Vorbereitungsmaßnahmen war es an der Zeit, dass Arjans Team das Gelände in der dicken Schicht aus frischem, sauberem Sand baureif machte. Die idealen Bedingungen für das Graben der neuen Fernwärmeleitungen waren gegeben. Mit einem elektrischen Kran, einem Limach E88.1, wurden die neuen Gräben sorgfältig ausgehoben. Verschiedene Längen und Durchmesser von Rohren, von PEØ110 bis PEØ250, werden sorgfältig spiegelgeschweißt. Eine präzise Aufgabe, denn alle Kurven und Winkel müssen in diesem zukünftigen Wohngebiet genau stimmen. Im nächsten Jahr werden hier nämlich Dutzende von Uferhäusern, Wallhäusern und Apartments gebaut, alle ohne Gasanschluss.
Die neuen, von Arjans Team installierten Leitungen werden all diese Wohnungen mit Warmwasser versorgen. In der Regel entsteht das warme Wasser für die Fernwärme durch Abwärme von beispielsweise Elektrizitätswerken oder Erdwärme aus einigen Kilometern Tiefe. Die Temperatur dieses Warmwassers beträgt normalerweise etwa 80 bis 90 Grad Celsius. Um dieses warme Wasser zu transportieren, verwenden wir oft isolierte Stahlrohre, die vor Ort geschweißt werden.
Hier ist es jedoch anders: Es handelt sich um ein Niedertemperatur-Wärmenetz von Warmtenetwerk Harderwijk. Das Wasser, das dieses Viertel speist, kommt mit einer konstanten Vorlauftemperatur von etwa 14 Grad Celsius an. Die Wärme stammt von der Abwärme der nahegelegenen Kläranlage. Alle Häuser im Viertel erhalten eine eigene Wärmepumpe, die das eingehende Wasser auf die erforderliche Temperatur für die Beheizung des Hauses erwärmt.
Da das Wasser mit einer niedrigeren Temperatur ankommt, genügen 100% Kunststoff- (PE-) Leitungen ohne Stahl. Diese Leitungen können daher spiegelgeschweißt werden, was sich stark vom herkömmlichen Schweißen unterscheidet. Beim Spiegel-schweißen werden die Rohre durch Erhitzen mit einem Heizelement (ähnlich einem großen Bügeleisen) so weit geschmolzen, dass sie nahezu flüssig sind. Die Enden der zu verschweißenden Teile werden dann mit leichtem Druck in einer eigens dafür vorgesehenen Form zusammengepresst, wodurch sie verschmelzen und eine feste Verbindung entsteht.
Alle erforderlichen Geräte zum Spiegel-schweißen werden nachhaltig durch einen speziellen Solaranhänger mit Energie versorgt. Dieser Anhänger verfügt über mehrere Akkupacks, die von einer großen Solarpanelfläche aufgeladen werden. Die Fläche der Solarpanels wird um das Dreifache vergrößert, wenn sie aufgestellt und ausgeklappt werden. Ein großartiges platzsparendes System, das die Effizienz und Einsatzmöglichkeiten des Anhängers erhöht.
Arjan fügt hinzu: „Wenn an dunklen Tagen die Akkus unter 20 % der Batteriekapazität sinken, springt ein HVO-Generator ein. Dieser lädt die Akkus ganz gleichmäßig auf. Selbst nachts lädt der HVO-Generator die Akkus im Leerlauf mit niedriger Drehzahl bis zu 90 % auf. Der Hauptvorteil – neben der umweltfreundlicheren Wahl – ist die Ruhe auf der Baustelle. Beim Spiegel-schweißen wurden wir nicht durch einen lauten konventionellen Generator gestört. Das ist schon angenehm, wenn man den ganzen Tag damit arbeitet.“
Arjan genießt die Arbeit mit seinem Team. Die PE-Rohre werden wie warme Semmeln verlegt. Es ist jedoch eine Aufgabe für geduldige Menschen. Jede Schweißnaht muss mit großer Sorgfalt erstellt werden und hat zudem eine lange Abkühlzeit, bevor das nächste Rohr in der Form platziert werden kann, um die nächste Schweißnaht zu erstellen. Das sorgt dafür, dass auf der Baustelle auch Zeit und Raum für etwas Spaß bleibt, wie man bei dieser Mannschaft sehen kann.
Wenn alle Leitungen verlegt sind, ist es Zeit für einen spannenden Moment. Das gesamte System wird unter hohem Druck auf Lecks getestet. Obwohl letztendlich maximal 10 bar auf den Leitungen stehen, wird jetzt für den Test ganze 24 Stunden lang ein Druck von 13 bar auf die Leitungen ausgeübt. Immer ein spannender Moment, aber einer, dem Arjans Team mit Zuversicht entgegenblickt. Sie vertrauen auf ihre Arbeit und aufeinander.
Arjan blickt auf ein schönes Projekt zurück: „Wenn am Ende alles geschafft ist, hat man es doch gemeinsam wieder gut hinbekommen. Es ist schön, Teil eines solchen Projekts zu sein, bei dem ein altes Asbestgelände letztlich in ein nachhaltiges neues Wohnviertel am Wasser verwandelt wird. Und das alles mit Blick auf eine wunderschöne alte Mühle, das Dolfinarium und so nachhaltig wie möglich mit einem großartigen Team. Was will man mehr?“
Gibt es Fragen, besteht Interesse an weiteren Informationen über unsere Dienstleistungen oder soll ein Gespräch mit einem Spezialisten geführt werden? Dann gerne Kontakt mit uns aufnehmen. Wir stehen bereit und helfen gerne weiter.